アーク溶接とは?基礎知識と仕組みを解説!
- HOME
- ブログ
- 【POLASTAR-三次元計測】
- アーク溶接とは?基礎知識と仕組みを解説!
現代のものづくりにおいて、「強度」「耐久性」「コストパフォーマンス」を兼ね備えた接合技術は欠かせません。その中でも、アーク溶接は高い信頼性と汎用性を持つ技術として、建設業、自動車業、造船業など多くの業界で活用されています。
本記事では、アーク溶接の基本的な仕組みから、レーザー溶接との違い、メリット・デメリットについて解説します。
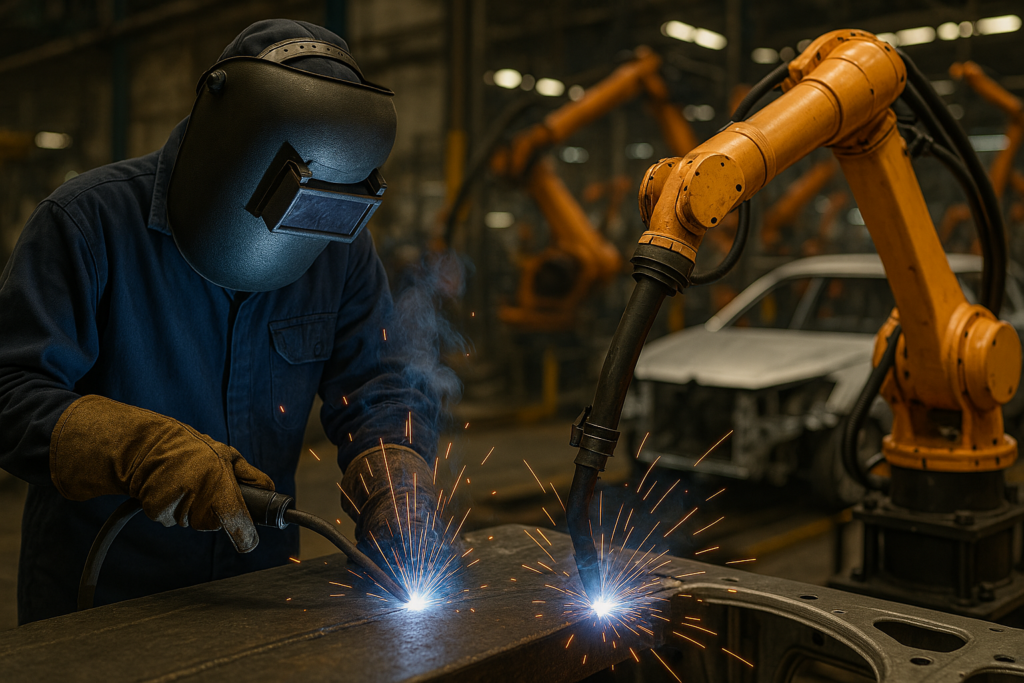
アーク溶接とは?
アーク溶接の特徴
- 多用途
アーク溶接は数千度の高温で、溶接を行うため鉄、アルミ、ステンレス、銅などさまざまな金属に適用でき、薄板から厚板まで幅広い材料に対応します。 - シールドが重要
溶接中に溶けた金属が大気中の酸素や窒素と反応しないように、シールドガスや被覆材を使って保護します。シールド方法によって溶接品質が大きく左右されます。シールドガスの種類によって、TIG溶接、MIG溶接、MAG溶接に分けられます。
アーク溶接の原理
①電気アークの発生
溶接棒(またはワイヤ)と母材の間に電圧をかけることで電流を流し、両者が一瞬離れたときにアーク放電が発生します。このアークが非常に高温(約4,000~6,000℃)になり、母材と溶加材(溶接棒やワイヤ)を溶かします。
②溶融池の形成
アークの熱で金属が溶け、溶融池(モルテンプール)が形成されます。溶融した金属が混ざり合うことで、一体化した接合部が作られます。
③シールドによる保護
アーク溶接では、酸素や窒素などの大気成分が溶融金属に悪影響を与えないようにシールド(保護)が必要です。
手溶接(被覆アーク溶接)では、溶接棒の被覆剤が燃焼してシールドガスを発生させ、ガスシールドアーク溶接(MIG/TIGなど)では外部からガス(アルゴンや二酸化炭素など)を供給します。仮にシールドガスがない状態となれば、酸化、不完全なビード、冷却不良、溶接の不安定性などが生じ、品質が大きく低下する可能性があります。
④凝固と溶接継手の形成
溶融池が冷却・凝固すると、金属同士が一体化し、強固な溶接継手が形成されます。適切な溶接技術を用いることで、強度の高い接合が可能になります。
アーク溶接の種類
アーク溶接にはいくつかの種類があります。アーク溶接で使用するガスの種類によって、TIG、MIG、MAG溶接を区別することができます。仕上がりや、自動溶接への適用性で使い分けられます。それぞれの特徴は以下の通りです。
溶接法 | 特徴 | 主な用途 | 自動溶接への適用性 |
---|---|---|---|
被覆アーク溶接 | シンプルな手動溶接、設備が安価、屋外作業に強い | 補修、建設現場、少量生産 | ✕ (手動が基本、自動化困難) |
MAG溶接 | 鉄鋼向け、自動化しやすく、スパッタ多めだが安定性あり | 製缶、建機、自動車部品 | ○ (ロボット適用が非常に多い) |
MIG溶接 | アルミ・ステンレス対応、スパッタが少なく美しい仕上がり | 自動車、薄板製品、装飾品など | ○ (自動化しやすい) |
TIG溶接 | 高品質なビード、美観重視、薄板や精密品向き | 医療・食品機器、航空部品 | △ (自動化は可能だが速度が遅め) |
アーク溶接とレーザー溶接の違い
アーク溶接と比較される技術として、レーザー溶接があります。レーザー溶接はレーザー光を照射して局所的に溶接する方法で、精密で歪みが少なく、細かい加工に適しています。
比較項目 | アーク溶接 | レーザー溶接 |
---|---|---|
コスト | 低い(設備が安価) | 高い(設備が高価) |
作業速度 | 速い(特にMIG/MAG) | さらに高速(特定用途で有利) |
精度・仕上がり | 一般的 | 高精度で歪みが少ない |
適用範囲 | 大規模構造物向け | 精密部品や薄板向け |
技術習得 | 比較的容易 | 高度な技術が必要 |
レーザー溶接は主に精密機械や電子部品の製造に適しており、アーク溶接は建設・自動車・造船などの大型構造物の接合に向いています。用途に応じて最適な技術を選ぶことが重要です。
レーザー溶接に関する記事はこちらもご覧ください。
まとめ
アーク溶接は、多様な業界で必要とされる高度な技術ですが、その品質は作業者のスキルや適切な設定、環境管理によって大きく左右されます。本記事で解説したメリット・デメリットを踏まえ、適切な作業方法を選択することで、安全かつ高品質な溶接を実現できます。さらに、作業効率の向上や溶接欠陥の低減を目指し、技術向上を継続的に行うことが重要です。
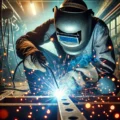
2025.05.26
溶接とは?溶接の種類とほかの接合方法との比較
この記事では、溶接の基本的な定義と、溶接方法の種類を紹介しています。アーク溶接、MIG溶接、TIG溶接などの手法が取り上げられ、それぞれの特徴や用途について解説。また、溶接とリベット接合やボルト接合、接着剤接合などの他の接合方法との比較も行い、最適な方法を選ぶための指針を示しています。…